Technical quality control
Quality Doesn’t Just Happen, It’s A Product Of Proper Project Management, A Lack Of Quality Control Makes It Impossible To Guarantee Quality In Your Projects. Using A Quality Checklist Ensure Quality Is Planned Into Your Project. By Implementing A Quality Checklist For All Your Projects, You Can “Check” Each Item Off As You Develop Your Project Plan. Rest Easy Knowing That You Have All Of Your Bases Covered Creating A Quality Control Inspection Checklist Should Be Among The First Steps You Take To Develop An Effective Quality Control Program. A Detailed Checklist Can Save You A Lot Of Trouble In The Long Run. It Can Defend Against Sub-Standard Or Non-Conforming Designs. Since This Document Is In Writing, It Can Also Serve As A Handy Reference Not Just For Engineers On The Design Office Floor, But Also For If You Have A Disagreement With The Client/ Stakeholders About Project Standards.
Getting An Absolutely Perfect Engineering Design Service Run Every Single Time Is Nearly Impossible. But You Can Bring That Goal Closer To Reality By Preventing Confusion And Conveying Expectations With A Clear QC Checklist.
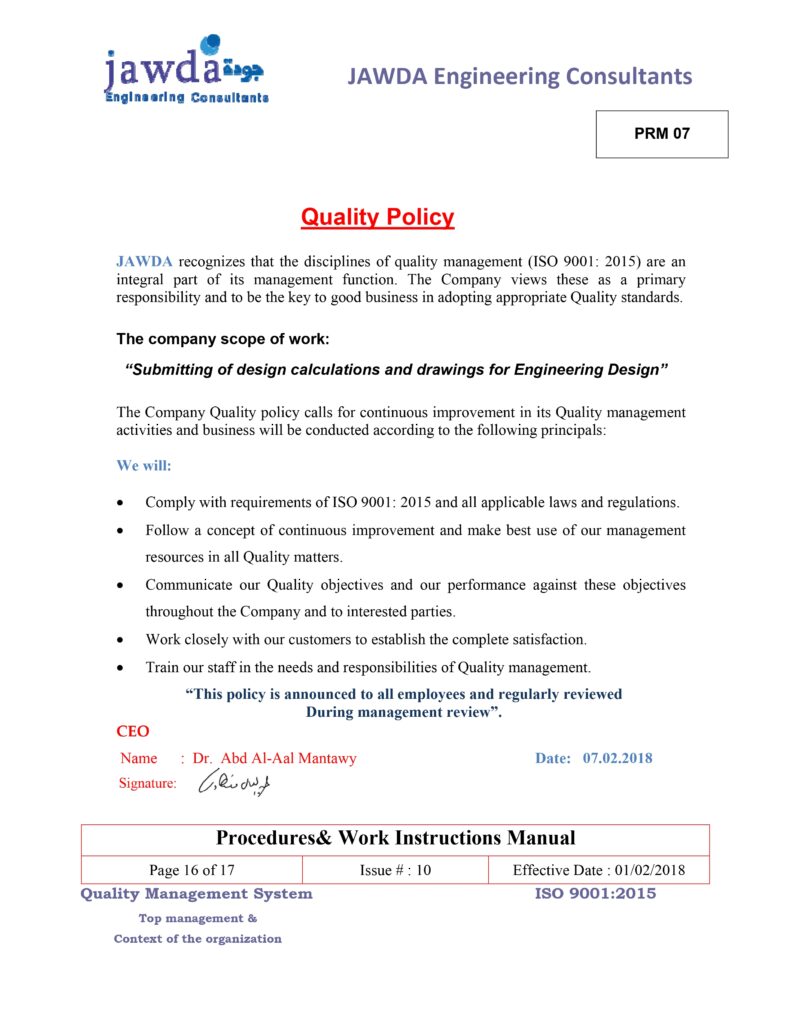
Technical quality control
In Jawda Engineering Consultant We Have Made Our Quality Control (QC) Handbook With Set Of Procedures Intended To Ensure That Our Performed Service Adheres To A Defined Set Of Quality Criteria Or Meets The Requirements Of Our Client
Our Project Quality Checklist Handbook Is A Tool Used To Aid The Project Team In Ensuring They Consider All Aspects Of Project And/Or Process Quality. With A Well-Planned And Repeatable Quality Management Is To Ensure The Delivery Of Our Design Services Which Are Acceptable To The Customer Based On Some Agreed Upon Standard Of Quality.
Our Quality Control Inspection Checklist Serves Two Main Purposes:
1.Outlining Quality Standards And Design Requirements The Client Is Expected To Meet
2.Providing Objective Criteria For Inspecting The Design Service To Ensure The Client’s Expectations Are Being Met
One Of The Less Obvious Benefits Of Collaborating With Our Client On Developing A Quality Control Inspection Checklist Is That We Can Improve Our Relationship With Our Client. Working On A Checklist Shows Them We Value Their Feedback. Additionally, Clients May Be Able To Suggest Ideas To Improve The Work Quality That Might Not Have Been Considered.
This Check-List Is A Companion To The Design Review Guidance Plan At Jawda, With The Help Of A Highly Qualified Engineering Review Team, We Perform The Design Review And Implement The Design Guide Lines And Work References. Our Handbook Of Our Quality Reference Is Under Continuous Development Base, To Keep Pace With Constant Changes And New Client’s Requests And Demands.
Work Environment
Office Employees Spend Majority Of Their Time Inside Work Stations And Offices, Where The Physical Environments Influence Their Well-Being And Directly Influence Their Work Performance And Productivity. In The Workplace, It Is Often Assumed That Employees Who Are More Satisfied With The Psychological And Physical Environment Are More Likely To Produce Better Outcomes. Collaboration Techniques, Flexibility With Employees, Issues Solving Methodology Are Among A Long List Of Criteria That Help JEC To Implement Optimum Psychological Environment To Help Employees Focus On The Service. JEC Applies A Special Methodology To Control Productivity Elements Instead Of Just Pushing Around To Get Things Done On Time. Our Methodology Incorporates The Management Of The Following Three Items;
1. Employees Favorite Environment
2. Work Load In Terms Of Time Management
3. Engineering Service And Related Quality
The Early Evaluation Of Those Three Items Defines The Expected Quality Of Service To Be Provided Under Certain Contract. Should The Actual Conditions Extends A Lower Quality, Our Team Leader(S) Will Immediately Design An Alternative Work Plan To Ensure Optimum Quality Of Service By Maintaining The Most Favorite Working Conditions For Our Employees, Fair Distribution Of Work And The Best Engineering Service As A Priority.
In Terms Of Physical Work Conditions; Temperature, Air Quality, Lighting And Noise Conditions In The Office Affect The Work Concentration And Productivity. Numerous Studies Have Consistently Demonstrated That Characteristics Of The Physical Office Environment Can Have A Significant Effect On Behavior, Perceptions And Productivity Of Employees.
Our Project Quality Checklist Handbook Is A Tool Used To Aid The Project Team In Ensuring They Consider All Aspects Of Project And/Or Process Quality. With A Well-Planned And Repeatable Quality Management Is To Ensure The Delivery Of Our Design Services Which Are Acceptable To The Customer Based On Some Agreed Upon Standard Of Quality.
Our Quality Control Inspection Checklist Serves Two Main Purposes:
1.Outlining Quality Standards And Design Requirements The Client Is Expected To Meet
2.Providing Objective Criteria For Inspecting The Design Service To Ensure The Client’s Expectations Are Being Met
One Of The Less Obvious Benefits Of Collaborating With Our Client On Developing A Quality Control Inspection Checklist Is That We Can Improve Our Relationship With Our Client. Working On A Checklist Shows Them We Value Their Feedback. Additionally, Clients May Be Able To Suggest Ideas To Improve The Work Quality That Might Not Have Been Considered.
This Check-List Is A Companion To The Design Review Guidance Plan At Jawda, With The Help Of A Highly Qualified Engineering Review Team, We Perform The Design Review And Implement The Design Guide Lines And Work References. Our Handbook Of Our Quality Reference Is Under Continuous Development Base, To Keep Pace With Constant Changes And New Client’s Requests And Demands.